【導(dǎo)讀】蘋果公司表示今年將在iPhone 8上使用OLED屏幕,其在智能手機等電子產(chǎn)品領(lǐng)域的示范效應(yīng)將是OLED的一重要推動力。隨著VR(虛擬現(xiàn)實)、可穿戴設(shè)備等新電子產(chǎn)品的爆發(fā)趨勢,OLED 將帶來新的切入點。 OLED 終端產(chǎn)品市場爆發(fā)迅速,帶動 OLED 增長前景可期,綜合來看,今年很有可能成為“OLED元年”。
比起傳統(tǒng)的液晶顯示(LCD)屏幕,被業(yè)界公認為下一代顯示技術(shù)的有機發(fā)光二極管(OLED,又被稱為有機電激光顯示)屏幕不僅具有全固態(tài)、輕薄、主動發(fā)光、高畫質(zhì)、低耗電等優(yōu)點,還可以用于嘗試透明、卷軸、折疊、曲面等突破傳統(tǒng)的屏幕形式,OLED是行業(yè)共同關(guān)注的未來顯示技術(shù)方向,但相對于應(yīng)用低溫多晶硅技術(shù)的中小尺寸OLED屏幕,應(yīng)用氧化物技術(shù)的大尺寸OLED屏幕在普及中遇到了眾多技術(shù)難點,目前受制于一些關(guān)鍵技術(shù)、成本及良品率偏低等因素影響,OLED面板規(guī)模性應(yīng)用及大尺寸產(chǎn)業(yè)化尚有較長一段進程。
采用OLED大屏幕的產(chǎn)品
面板、有機材料鍍膜及封裝為OLED大屏幕產(chǎn)品量產(chǎn)化的三大指標,由于開發(fā)大尺寸設(shè)備的瓶頸難以突破,低溫多晶矽(LTPS)面板制程難以跨越5.5代OLED面板生產(chǎn)線,因為這種技術(shù)是把紅、綠、藍有機發(fā)光體在玻璃面板上水平蒸鍍,由于在蒸鍍時必須要使用金屬遮罩,在做大面板時由于重力會造成金屬遮罩下沉及混色等問題,因此不適合實現(xiàn)大尺寸和高分辨率。鑒于此,非晶矽(a-Si)與氧化物薄膜晶體管(Oxide TFT)面板成為技術(shù)研發(fā)的選擇。不過,前者的電子移動速度太慢,會降低OLED面板的動態(tài)顯示反應(yīng)速度。因此,后者已成為技術(shù)研發(fā)的首選,但是一直以來,這項技術(shù)進展緩慢。好在氧化物薄膜晶體管面板材料與制程與非晶矽相近,所以,部分非晶矽既有制程設(shè)備可被氧化物薄膜晶體管所沿用。
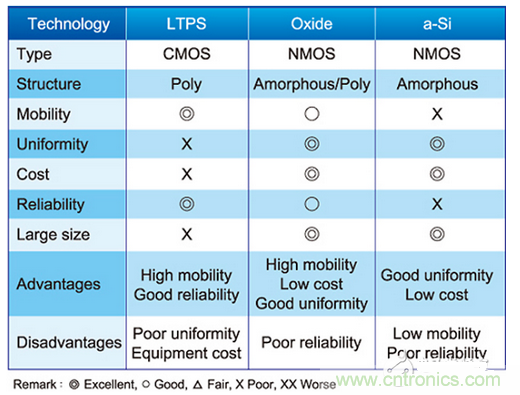
面板技術(shù)比較表
常見的氧化物半導(dǎo)體如氧化銦鎵鋅(InGaZnO),是一種電子移動率可達10平方厘米(cm2)/VS的新材料,為傳統(tǒng)非晶矽(《1cm2/VS)的數(shù)十倍以上。加上非晶(Amorphous)結(jié)構(gòu)可以在大尺寸獲得良好的均勻度,適合應(yīng)用在大尺寸面板,達到高清晰度、低能耗、低漏電的優(yōu)點,但其可靠度不 佳以及PMOS制造工藝困難一直是亟待改善的技術(shù),前者是量產(chǎn)商品化必須克服的重要關(guān)鍵,后者可用補償電路(CompensaTIon Circuit)加以克服。
采用OLED透明屏幕的產(chǎn)品
常見的氧化物薄膜晶體管元件結(jié)構(gòu)主要有共平面(Coplanar)、蝕刻阻障層(Island Stop/Etch Stop Layer,IS/ESL)和背通道蝕刻(Back Channel Etch,BCE)這三種。共平面結(jié)構(gòu)制程簡單,但因為氧化物半導(dǎo)體層要攀爬源汲極金屬,容易導(dǎo)致電特性與接觸問題,且可靠度不 佳。至于背通道蝕刻和蝕刻阻障層結(jié)構(gòu)在元件特性及制程良品率上則較具優(yōu)勢,尤其是背通道蝕刻結(jié)構(gòu)相容于標準非晶矽結(jié)構(gòu),極具競爭力。但若考量可靠度,則以蝕刻阻障層結(jié)構(gòu)最為理想,原因主要在于蝕刻阻擋層可保護元件的背通道,不受制程影響產(chǎn)生特性 差異,但缺點是復(fù)雜的制程導(dǎo)致成品與良品率問題。
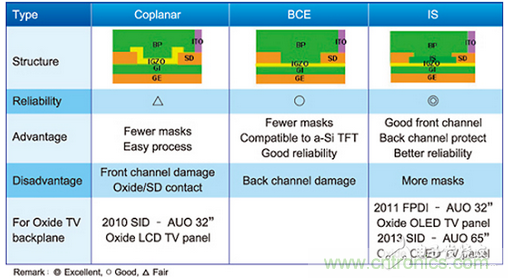
常見的氧化物薄膜晶體管元件結(jié)構(gòu)比較表
氧化物薄膜晶體管技術(shù)的重要性在于其量產(chǎn)機型相容于現(xiàn)有主流技術(shù)非晶硅的設(shè)備,由于氧化物薄膜晶體管材料特性對光與熱會導(dǎo)致電特性的改變,即臨界電壓偏移(Threshold Voltage Shift,Vth Shift),甚至可以運用在光感應(yīng)器(Photo Sensor)上,所以如何改善均勻度與可靠度將是一大難題,制程的調(diào)校相當困難與敏感,制程穩(wěn)定度要求也相對高。通過與試驗室的持續(xù)分析與改進,研究人員在氧化物技術(shù)上,研發(fā)試制線的整面OLED的臨界電壓偏移值已經(jīng)小于0.8伏特。經(jīng)過面板可靠度測試,發(fā)現(xiàn)使用壽命預(yù)估可超過10年,已經(jīng)超越傳統(tǒng)非晶硅技術(shù),相當接近于低溫多晶矽技術(shù)。
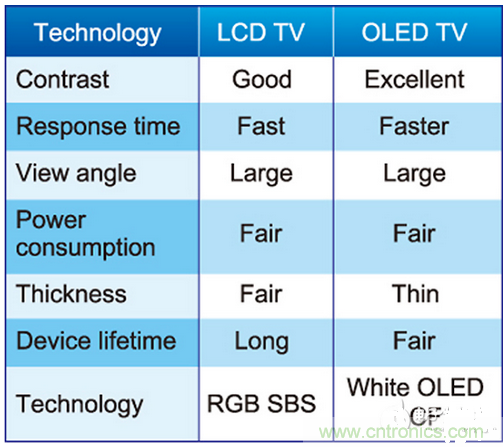
LCD與OLED特性比較表
OLED屏幕采用紅、綠、藍(R、G、B)像素組成,其使用主流的有機材料鍍膜技術(shù)——真空蒸鍍注,這種制作方式要平衡每個像素內(nèi)紅、綠、藍有機發(fā)光體的放置量,維持亮度的均勻性,隨著OLED屏幕尺寸加大,會導(dǎo)致生產(chǎn)良品率下降,由于藍色有機發(fā)光體的壽命短,為了修復(fù)其缺陷,會稍微多蒸鍍一點藍色OLED有機發(fā)光體,但導(dǎo)致的結(jié)果是紅、綠、藍像素構(gòu)造中的色彩歪曲現(xiàn)象。除因蒸鍍槽設(shè)計緣故,致使蒸鍍技術(shù)的生產(chǎn)效率欠佳之外,也面臨適使用8代OLED面板生產(chǎn)線的蒸鍍設(shè)備的難產(chǎn)窘境。除繼續(xù)采用5.5代線生產(chǎn)OLED面板之外,也可以改用雷射技術(shù)進行有機材料鍍膜,或采用氧化物面板和白光OLED搭配彩色濾光片濾出紅、藍、綠三原色,較接近現(xiàn)行的液晶顯示屏幕制程,即將紅、綠、藍有機發(fā)光體在整片白光OLED面板上垂直蒸鍍,通過色彩提純技術(shù)來表現(xiàn)色彩信息,鍍膜后再透過擴散膜達成均勻的面光源,這種方式在蒸鍍有機物時由于不使用金屬遮罩,所以不受面板尺寸限制,可以均勻蒸鍍有機物,并且是通過垂直蒸鍍紅、綠、藍有機發(fā)光體進行色彩提升的構(gòu)造,所以藍色有機發(fā)光體的壽命問題得到了很好的解決,雖然其色彩表現(xiàn)相對較差且耗電,但良品率相對較高,易于量產(chǎn)。
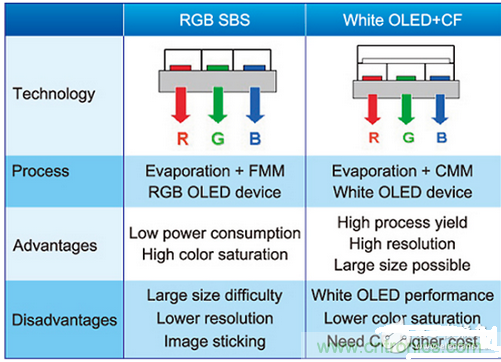
常見全彩OLED技術(shù)比較表
常見全彩OLED技術(shù)主要包含紅、綠、藍像素并置法(RGB-SBS,Side-By-Side)以及白光OLED+彩色濾光片(White OLED+Color Filter)技術(shù)。紅、綠、藍像素并置法由紅、綠、藍像素分別發(fā)光所組成,不僅能獲得較佳的色彩飽和度,還能省電,但大尺寸蒸鍍(EvaporaTIon)不易,需要持續(xù)開發(fā)。
雖然制程相對較難的精細金屬遮罩(Fine Metal Mask,F(xiàn)MM,也叫精細金屬掩膜板)像素技術(shù)的色彩表現(xiàn)較佳、省電,但立刻就會遇到大尺寸化的挑戰(zhàn),包括挑戰(zhàn)精細金屬遮罩與無混色(Color Mixing)需求,以及挑戰(zhàn)溫度超過1000℃以上的金屬蒸鍍制程。研究人員嚴格地執(zhí)行制程控制,有效率地回饋制程參數(shù),并且搭配精細分片(Fine Divided Sheet,F(xiàn)DS)技術(shù)后,終于成功開發(fā)出不混色技術(shù),達成前端氧化物薄膜晶體管與后端OLED皆可全板(Full Sheet)制作的里程碑。
采用OLED曲面屏幕的產(chǎn)品
自從串級式(Tandem)OLED結(jié)構(gòu)被發(fā)表后,高效率白光OLED已經(jīng)逐步成真,并且隨著材料與元件的技術(shù)演進,白光OLED技術(shù)已到達照明領(lǐng)域與顯示器領(lǐng)域上可被接受的水準。然而,相較于采用紅、綠、藍像素并置法的OLED的廣色域與高色純度,白光OLED元件卻難以望其項背。除此之外,組成白光元件至少需要10層膜以上,在長時間下,每一片OLED元件上的膜的厚度均一性也是金屬蒸鍍設(shè)備上亟待解決的一大問題。
采用OLED大屏幕的產(chǎn)品
近幾年來,除材料演進外,OLED元件技術(shù)的提升是整個OLED產(chǎn)業(yè)成功的一大關(guān)鍵。元件首重光學(xué)厚度設(shè)計,最佳化后的光學(xué)厚度能讓有機發(fā)光材料所發(fā)出的顏色與發(fā)光效率達到最佳化,同時根據(jù)產(chǎn)品的屬性規(guī)劃出上或下發(fā)光元件與強或弱共振腔(Cavity)。OLED元件在設(shè)計上使用多層傳輸層與新型藍色發(fā)光材料,因此,在弱共振腔的下發(fā)光元件上獲得高效率與好的藍色色度表現(xiàn),在CIE1931色座標下會呈現(xiàn)出83%色域的表現(xiàn),并且在元件發(fā)光效率上由于多傳輸層的應(yīng)用,顯著提升熒光發(fā)光層材料三重態(tài)能階(Triplet State)上的能量回收,因此提升了元件的效能。另外,OLED元件搭載OLED像素補償電路專利技術(shù)(OLED Engine),可有效改善氧化物薄膜晶體管及OLED的臨界電壓偏移所導(dǎo)致的亮度不均勻。
為實現(xiàn)更輕薄與低成本的OLED屏幕,要用可量產(chǎn)型的薄膜封裝技術(shù)取代傳統(tǒng)的玻璃封裝技術(shù)。OLED屏幕是結(jié)合上下面板組合而成的,在傳統(tǒng)工藝方面,上面板普遍采用玻璃封裝,然而兼具重量輕、可實現(xiàn)薄型化及低成本的薄膜封裝技術(shù)是大勢所趨。由于低溫多晶矽面板的制程溫度高達600℃,玻璃面板的耐高溫性不佳,因此,OLED玻璃面板耐熱性受技術(shù)束縛。為提高低溫多晶矽面板制程的良品率,縮短OLED屏幕的量產(chǎn)時間,OLED玻璃面板企業(yè)生產(chǎn)出適用于低溫多晶矽高溫制程的荷花玻璃(Lotus Glass),這種玻璃面板具有零雜質(zhì)、高平坦度及耐熱穩(wěn)定性的特點,以供應(yīng)部分現(xiàn)有的4.5、5.5代OLED面板生產(chǎn)線制造。
目前,有機光電子學(xué)在材料、功效、壽命、彩色化、大尺寸、柔性化、封裝和生產(chǎn)工藝等方面尚有一系列理論、技術(shù)和工藝問題亟待解決,這些環(huán)節(jié)上存在的不足都相當程度地制約了有機光電功能材料與技術(shù)在產(chǎn)業(yè)化方向的發(fā)展。其中,OLED技術(shù)要達到大規(guī)模的應(yīng)用,取決于材料、設(shè)計和制備工藝等的全面進步,還需要對材料和器件結(jié)構(gòu)進行創(chuàng)新,以提高功效、增加穩(wěn)定性和降低成本。
注:真空蒸鍍——在真空環(huán)境下將有機材料放在坩鍋中加熱,使之蒸發(fā)并在覆蓋有掩膜板(MASK)的玻璃基板上沉積成膜的技術(shù),是目前最成熟,也是目前被量產(chǎn)的小尺寸有源驅(qū)動(AMOLED)產(chǎn)品基本都采用的有機成膜技術(shù),但精細金屬遮罩像素技術(shù)存在掩膜板與玻璃基板的對位精度要求高、掩膜板因重力及熱膨脹容易變形、材料利用率低等問題。