- OLED技術原理
- OLED技術主要特點
- 技術發(fā)展瓶頸
- OLED產(chǎn)業(yè)化進程
- 低成本其工藝簡單
- 自發(fā)光不需要背光源
- 全固態(tài)無真空腔,無液態(tài)成份
- 快速響應響應時間為微秒級
OLED技術原理
OLED是指有機半導體材料和有機發(fā)光材料在電場的驅動下,通過載流子注入和復合導致發(fā)光的技術。其原理是用ITO玻璃透明電極和金屬電極分別作為器件的陽極和陰極,在一定電壓驅動下,電子和空穴分別從陰極和陽極注入到電子傳輸層和空穴傳輸層,然后分別遷移到發(fā)光層,相遇后形成激子使發(fā)光分子激發(fā),后者經(jīng)過輻射后發(fā)出可見光。輻射光可從ITO一側觀察到,金屬電極膜同時也起了反射層的作用。下圖是一個簡單的OLED器件結構示意圖。
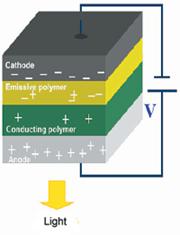


[page]
根據(jù)使用有機功能材料的不同,OLED器件可以分為兩大類:小分子器件和高分子器件。小分子OLED技術發(fā)展較早(1987年),而且技術已經(jīng)達到商業(yè)化生產(chǎn)水平;高分子OLED又被稱為PLED(PolymerLED),其發(fā)展始于1990年,目前該技術尚未成熟。
根據(jù)驅動方式的不同,OLED器件可以分為無源驅動型(又稱被動驅動PM,PassiveMatrix)和有源驅動型(又稱主動驅動AM,ActiveMatrix)兩種。無源驅動型不采用薄膜晶體管(TFT)基板,一般適用于中小尺寸顯示;有源驅動型則采用TFT基板,適用于中大尺寸顯示,特別是大尺寸全彩色動態(tài)圖像的顯示。目前,無源驅動型OLED技術已經(jīng)比較成熟,商業(yè)化的產(chǎn)品都是無源驅動型;有源驅動型OLED技術發(fā)展很快,但還需要幾年的時間才能推出商用產(chǎn)品。
OLED顯示屏的制備工藝流程主要包括四個步驟,如上圖所示。
OLED技術主要特點
有機發(fā)光顯示器件之所以受到人們的青睞,是因為其與LCD為代表的第二代顯示器相比,有著突出的技術優(yōu)點(見表1):
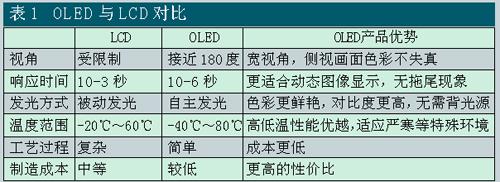
●低成本其工藝簡單,使用原材料少。使人們相信OLED將成為LCD替代性技術的最重要原因是其在降低加工成本方面的潛力。除了對材料和工藝方面的要求比LCD低近1/3外,OLED的加工工藝也比LCD簡單得多。據(jù)相關資料顯示,OLED顯示屏需要86道加工工序,而LCD屏則需要200多道工序。在成本決定生命力的未來大屏幕顯示領域,這無疑增加了OLED競爭的砝碼。
●自發(fā)光不需要背光源。
●低壓驅動和低功耗直流驅動電壓在10伏以下,易用于便攜式移動顯示終端上。
●全固態(tài)無真空腔,無液態(tài)成份,機械性能好,抗震動性強,可實現(xiàn)軟屏顯示。使用塑料、聚酯薄膜或膠片作為基板,OLED屏可以做到更薄,甚至可以折疊或卷起來。目前由于在軟基板上的涂鍍等加工工藝還未成熟,可折疊或卷曲的顯示器產(chǎn)品還沒有商品化,但這一切都會在不遠的將來實現(xiàn)。
●快速響應響應時間為微秒級,是普通液晶顯示器響應時間的1/1000,適于播放動態(tài)圖像,具有寬視角特性,上下、左右的視角寬度超過170度。
●高效發(fā)光可作為新型環(huán)保光源。
●寬溫度范圍在-40℃~80℃范圍內都可正常工作。
●高亮度顯示效果鮮艷、細膩。
[page]
技術瓶頸
影響OLED技術發(fā)展的最大障礙是器件壽命和材料穩(wěn)定性問題。目前,彩色OLED的壽命還只能達到5000小時,這使應用受到了限制。不過,由于其發(fā)展前景被看好,目前全球從事OLED研究的機構和廠商多達90多家。由于各家技術之間存在著很大差異,材料有小分子和高分子OLED兩種,驅動方式分為主動和被動,而彩色顯示的實現(xiàn)原理又有采用三色不同材料、采用三色濾色膜、采用色變換等多達6種方式,再加上涂鍍、噴繪等多種加工工藝,OLED技術的實現(xiàn)可謂是真正意義上的百花齊放。對于一種萌芽期的技術,盡管這有利于技術的健康發(fā)展,但研發(fā)力量的分散和技術的爭議在一定程度上會延緩技術發(fā)展的步伐。
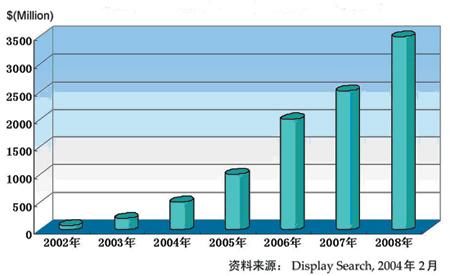
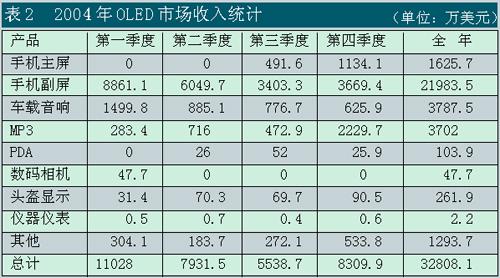
根據(jù)全球權威平板顯示器(FPD)市場調研和咨詢機構DisplaySearch在2004年12月的最新統(tǒng)計(見表2),OLED行業(yè)2004年全年總收入為3.28億美元,比2003年增長了41%。上圖為DisplaySearch2004年2月對全球OLED市場的預測。
OLED已進入的產(chǎn)品領域包括手機主屏和副屏、汽車音響、MP3、工業(yè)儀表、PDA、車載儀表、數(shù)碼相機和微顯示器(MicrodisplayforNearEyeApplication)等領域。其中,手機副屏約為2.2億美元,占67%,汽車音響約為0.38億美元,占11.6%,MP3屏為0.37億美元,占11.3%,這三者共占了約90%。
[page]
OLED產(chǎn)業(yè)化進程
1.全球發(fā)展概況
OLED的產(chǎn)業(yè)化已經(jīng)起步,今后的3~5年是發(fā)展的關鍵時期。雖然OLED技術起源于歐美,但因為成本和產(chǎn)業(yè)鏈的關系,最終實現(xiàn)大規(guī)模產(chǎn)業(yè)化的國家和地區(qū)卻集中在東亞,主要是日本、韓國、中國大陸和臺灣。
目前,日本Pioneer有3條生產(chǎn)線,其中2條PM-OLED線、1條AM-OLED線,月產(chǎn)能120萬片。三星SDI的OLED月產(chǎn)量為150萬片,并計劃建成AM-OLED(370×470)專用生產(chǎn)線。中國臺灣的錸寶現(xiàn)有7條生產(chǎn)線,今年計劃再引進2條線,月產(chǎn)能130萬片,錸寶OLED今年出貨目標為1200萬~1500萬片。除了以上3家外,LG電子、韓國大宇、CPT和聯(lián)宗光電等公司都在積極投資建設OLED生產(chǎn)線,希望早日進入OLED市場。
2.我國發(fā)展概況
(1)成果顯著
在過去的幾年里,我國在OLED機理研究和器件結構設計等方面做了大量工作,目前從事OLED研發(fā)和產(chǎn)業(yè)化的機構及企業(yè)主要有:清華大學、華南理工大學、吉林大學、上海大學、東南大學、香港城市大學、香港科技大學、長春光機所、中科院化學所、北京維信諾科技有限公司、信利半導體、上海航天上大歐德公司、上海廣電電子集團、深圳先科集團、TCL、五糧液集團、中國普天集團等。
清華大學于1996年成立了OLED項目組,設計安裝了中國大陸第一臺OLED蒸鍍設備,建成了中國大陸第一個OLED超凈實驗室(見圖5)。2001年,由于獲得原國家計委的支持,清華大學及其他單位合資成立了北京維信諾科技有限公司,建成了中國大陸第一條OLED中試生產(chǎn)線(見圖6),2003年開始有小批量單色產(chǎn)品進入市場的儀器儀表領域,成為中國大陸第一家能夠生產(chǎn)和銷售自產(chǎn)OLED產(chǎn)品的公司,產(chǎn)品獲得多家客戶的認可。2002年,維信諾與清華大學成立了聯(lián)合實驗室,共同開發(fā)有機發(fā)光顯示技術。截至2005年3月,維信諾科技聯(lián)合清華大學有機光電聯(lián)合實驗室共同申請了46項專利,其中有8項國際專利,內容覆蓋材料、器件結構、器件工藝和驅動電路等技術領域,至今,已有20項專利獲得授權,擁有十多項核心專利技術。此外,在中試生產(chǎn)線上,維信諾科技突破并掌握了批量生產(chǎn)的關鍵技術,豐富和積累了大量OLED量產(chǎn)工藝及技術Know-how,完善了技術成果向產(chǎn)業(yè)化的充分轉化。
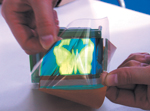
圖1北京維信諾科技有限公司研制出的OLED軟屏
清華大學和維信諾公司先后承擔了國家計委、國家發(fā)改委、科技部“863”計劃、信息產(chǎn)業(yè)部和北京市科委等多個重大重點創(chuàng)新項目,開發(fā)出高清晰度26萬色96×64、128×160全彩OLED和單色128×64柔軟點陣OLED顯示屏樣品,研究成果達到國際先進水平。目前,維信諾公司正在進行OLED大規(guī)模生產(chǎn)線的籌備,預計2006年建成投產(chǎn)第一條PMOLED生產(chǎn)線。
上海大學于1990年開始OLED的研究工作,已研制出白色發(fā)光器件和綠色矩陣顯示器件。綠色器件的半亮度壽命已達到14000小時,紅色器件半亮度壽命為7500小時,藍色器件半亮度壽命為1016小時,白色器件半亮度壽命大于2000小時。上海大學與中國航天科工集團公司于2001年9月聯(lián)合組建了“上海航天上大歐德科技有限公司”,以進行OLED的中試研究和批量生產(chǎn)。
吉林大學從1994年開始在新型OLED材料開發(fā)及性能研究方面開展了深入系統(tǒng)的研究工作,在新型電致發(fā)光配合物材料方面取得了一些有創(chuàng)新性的成果,尤其在藍光配合物材料方面取得了一些突破,還研制出96×64像素、分辨率為3條線/毫米的有機發(fā)光顯示屏。
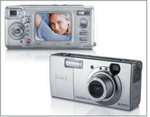
圖2柯達推出的全球第一款OLED屏數(shù)碼相機
[page]
在TFT技術方面,吉林省彩晶數(shù)碼高科顯示器有限公司目前已具備制作供大面積平板顯示器使用的非晶硅TFT技術和設備,其成品率可以達到80%以上,為我國開展低溫多晶硅TFT-OLED的研究打下了良好基礎。
中科院長春光機與物理所在稀土發(fā)光材料的研究方面取得重大進展,1996年開展非晶硅TFT器件研究工作,1999年開始進行多晶硅TFT驅動技術的研究工作并取得初步結果。
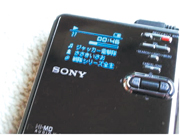
圖3SonyMZ-RH10MD,這是MD中第一次采用5行OLED屏幕
華中科技大學從20世紀80年代末開始開展非晶硅TFT有源矩陣液晶顯示器的研究,在非晶硅、多晶硅薄膜和TFT的研究與制備、AMLCD和多晶硅TFT集成一體化技術方面,具備了良好基礎。
成都電子科技大學通過多年來的科研工作,在材料、器件和低溫多晶硅TFT等方面取得了一定進展。
南開大學與香港科技大學合作,于去年獲得了一項國家自然科學基金委聯(lián)合探索研究多晶硅TFT-OLED的項目,現(xiàn)已就TFT驅動單元的新型結構和矩陣特性進行從多晶硅TFT物理模型的建立到模擬計算和仿真的研究工作。
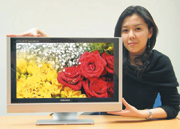
圖42005年1月三星推出了21英寸OLED面板
北方交通大學在多年研究無機電致發(fā)光的基礎上,在有機/無機復合發(fā)光器件的研究方面取得了一些創(chuàng)新性成果。華南理工大學在高分子材料制備方面取得了顯著進展,合成出了紅綠藍三基色高分子熒光材料,紅光材料的點致發(fā)光(EL)效率達到2.5%。另外,中科院化學所、長春應化所、華東理工大學在新型小分子發(fā)光材料和高分子發(fā)光材料方面進行了大量的研究,并取得了一些重要的研究成果。
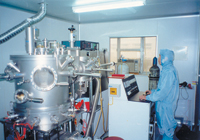
圖5中國大陸第一個OLED超凈實驗室
在產(chǎn)業(yè)化方面,信利半導體2003年引進了一條小批量OLED生產(chǎn)線,目前正在進行產(chǎn)品及市場方面的開發(fā),信利計劃今年年底開始引進大規(guī)模生產(chǎn)線,明年10月份投產(chǎn)。
(2)技術差距及原因分析
目前我國OLED的技術和產(chǎn)業(yè)化整體水平與國外仍有兩年左右的差距,但是在部分核心技術上已經(jīng)具有國際先進水平,取得了一定的研究成果。
例如,在器件結構方面,我國開發(fā)的單層結構器件突破了傳統(tǒng)的雙層和多層結構專利技術,減少材料、設備和工藝過程,大大降低了成本;在材料方面,吉林大學在世界范圍內率先開展了三線態(tài)磷光材料的性能研究,維信諾和清華大學聯(lián)合開發(fā)的具有自主知識產(chǎn)權的紅光材料在啟動電壓為2.4V時,最高亮度達到7280cd/m2,而國外的紅光材料在啟動電壓為3.5V時,最高亮度只能達到4300cd/m2;在OLED的彩色化方面,我國也已經(jīng)開發(fā)出高清晰度26萬色全彩OLED樣品,追上了世界水平;在大尺寸顯示屏開發(fā)方面,國外已經(jīng)開發(fā)出24.2英寸的小分子OLED樣品和40英寸的高分子OLED樣品,但是大尺寸技術還不成熟,壽命和成品率問題估計還需5~10年的時間才能解決。
但同國際前沿有機發(fā)光顯示技術比較,我國還存在一些明顯的技術差距,其突出表現(xiàn)為:有機發(fā)光紅綠藍三色材料解決方案不完善,無法提供具備實用性的藍光發(fā)光材料,磷光材料的紅綠藍三色實用化材料還沒有開發(fā)成功。我國有機發(fā)光顯示材料的研發(fā)和生產(chǎn)脫節(jié),研發(fā)機構有很多,但是OLED材料的生產(chǎn)廠商卻極少,更缺少有機發(fā)光顯示材料的下游廠商,材料評估和產(chǎn)業(yè)化有障礙。與國外相比,我國有機發(fā)光顯示材料方面擁有的知識產(chǎn)權較少,需要加快研發(fā)進度。在驅動IC方面,全球已經(jīng)有多家公司在從事OLED驅動IC的設計和生產(chǎn),而我國只能從國外引進驅動IC;在大尺寸和彩屏技術上,由于設備條件相對落后,資金投入相對缺乏,目前還同國外發(fā)展有很大差距。這些環(huán)節(jié)上存在的不足,都一定程度地制約了我國有機發(fā)光技術的發(fā)展。
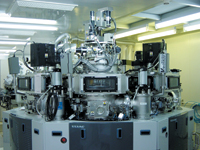
圖6中國大陸第一個OLED中試線
(3)產(chǎn)業(yè)差距及原因分析
目前,我國只有兩條OLED中試線,推出了單色OLED產(chǎn)品。而國外已經(jīng)有OLED生產(chǎn)線十幾條,推出了64K色、多色和單色OLED產(chǎn)品。有機發(fā)光顯示ITO玻璃國產(chǎn)化方面,目前國內還沒有一家能夠生產(chǎn)符合用于OLED生產(chǎn)的ITO玻璃。北京維信諾公司正在與國內一些廠家聯(lián)合攻關,力爭盡快實現(xiàn)ITO玻璃的國產(chǎn)化。除此之外,光刻膠等原材料也都存在類似的問題。
在生產(chǎn)設備方面,我國雖然有OLED生產(chǎn)設備的制造廠商,但是OLED的關鍵生產(chǎn)設備技術掌握在日本、韓國手中,我國只有通過進口才能得到。
在生產(chǎn)方面,由于我國TFT發(fā)展滯后,面板的制備技術薄弱,生產(chǎn)管理經(jīng)驗積累不足,因此在AMOLED的生產(chǎn)工藝開發(fā)方面難度較大,同時也缺乏OLED生產(chǎn)管理人才,這是我國OLED產(chǎn)業(yè)化建設的弱點。
總之,我國OLED上下游產(chǎn)業(yè)鏈尚不完備,OLED技術本身還沒有完全成熟,與國外的差距沒有TFT-LCD和PDP大。國內正在研發(fā)OLED的單位較多,有多條完整的試驗線,但研發(fā)內容重復較多,差異性小,還沒有形成特色;已有小尺寸彩色無源樣品開發(fā)技術,正在開發(fā)單色小尺寸產(chǎn)品生產(chǎn)技術,有源技術難度較大;原材料的開發(fā)較活躍,但還沒有篩選出綜合性能較好的材料;OLED高素質的技術和管理人才緊缺,存在政府和企業(yè)對OLED的資金投入不夠等,這些都制約了我國OLED產(chǎn)業(yè)化的進展。