- 焊點(diǎn)的失效模式
- 影響無鉛焊點(diǎn)可靠性的因素
- 無鉛焊點(diǎn)可靠性測試方法
隨著電子信息產(chǎn)業(yè)的日新月異,微細(xì)間距器件發(fā)展起來,組裝密度越來越高,誕生了新型SMT、MCM技術(shù),微電子器件中的焊點(diǎn)也越來越小,而其所承載的力學(xué)、電學(xué)和熱力學(xué)負(fù)荷卻越來越重,對可靠性要求日益提高[1]。電子封裝中廣泛采用的SMT封裝技術(shù)及新型的芯片尺寸封裝(CSP)、焊球陣列(BGA)等封裝技術(shù)均要求通過焊點(diǎn)直接實(shí)現(xiàn)異材間電氣及剛性機(jī)械連接(主要承受剪切應(yīng)變),它的質(zhì)量與可靠性決定了電子產(chǎn)品的質(zhì)量。
一個(gè)焊點(diǎn)的失效就有可能造成器件整體的失效,因此如何保證焊點(diǎn)的質(zhì)量是一個(gè)重要問題。傳統(tǒng)鉛錫焊料含鉛,而鉛及鉛化合物屬劇毒物質(zhì),長期使用含鉛焊料會給人類健康和生活環(huán)境帶來嚴(yán)重危害。
目前電子行業(yè)對無鉛軟釬焊的需求越來越迫切,已經(jīng)對整個(gè)行業(yè)形成巨大沖擊。無鉛焊料已經(jīng)開始逐步取代有鉛焊料,但無鉛化技術(shù)由于焊料的差異和焊接工藝參數(shù)的調(diào)整,必不可少地會給焊點(diǎn)可靠性帶來新的問題。因此,無鉛焊點(diǎn)的可靠性也越來越受到重視。本文敘述焊點(diǎn)的失效模式以及影響無鉛焊點(diǎn)可靠性的因素,同時(shí)對無鉛焊點(diǎn)可靠性測試方法等方面做了介紹。
焊點(diǎn)的失效模式
焊點(diǎn)的可靠性實(shí)驗(yàn)工作,包括可靠性實(shí)驗(yàn)及分析,其目的一方面是評價(jià)、鑒定集成電路器件的可靠性水平,為整機(jī)可靠性設(shè)計(jì)提供參數(shù);另一方面,就是要提高焊點(diǎn)的可靠性。這就要求對失效產(chǎn)品作必要的分析,找出失效模式,分析失效原因,其目的是為了糾正和改進(jìn)設(shè)計(jì)工藝、結(jié)構(gòu)參數(shù)、焊接工藝等,焊點(diǎn)失效模式對于循環(huán)壽命的預(yù)測非常重要,是建立其數(shù)學(xué)模型的基礎(chǔ)。下面介紹3種失效模式。
1焊接工藝引起的焊點(diǎn)失效
焊接工藝中的一些不利因素及隨后進(jìn)行的不適當(dāng)?shù)那逑垂に嚳赡軙?dǎo)致焊點(diǎn)失效。SMT焊點(diǎn)可靠性問題主要來自于生產(chǎn)組裝過程和服役過程。在生產(chǎn)組裝過程中,由于焊前準(zhǔn)備、焊接過程及焊后檢測等設(shè)備條件的限制,以及焊接規(guī)范選擇的人為誤差,常造成焊接故障,如虛焊、焊錫短路及曼哈頓現(xiàn)象等。
另一方面,在使用過程中,由于不可避免的沖擊、振動(dòng)等也會造成焊點(diǎn)的機(jī)械損傷,如波峰焊過程中快速的冷熱變化對元件造成暫時(shí)的溫度差,使元件承受熱一機(jī)械應(yīng)力。當(dāng)溫差過大時(shí),導(dǎo)致元件的陶瓷與玻璃部分產(chǎn)生應(yīng)力裂紋。應(yīng)力裂紋是影響焊點(diǎn)長期可靠性的不利因素。
同時(shí)在厚、薄膜混合電路(包括片式電容)組裝過程中,常常有蝕金、蝕銀的現(xiàn)象。這是因?yàn)楹噶现械腻a與鍍金或鍍銀引腳中的金、銀形成化合物,從而導(dǎo)致焊點(diǎn)的可靠性降低。過度的超聲波清洗也可能對焊點(diǎn)的可靠性有影響。
2時(shí)效引起的失效
當(dāng)熔融的焊料與潔凈的基板相接觸時(shí),在界面會形成金屬間化合物(intermetallicCompounds)。在時(shí)效過程中,焊點(diǎn)的微結(jié)構(gòu)會粗化,界面處的IMC亦會不斷生長。焊點(diǎn)的失效部分依賴于IMC層的生長動(dòng)力學(xué)。界面處的金屬間化合物雖然是焊接良好的一個(gè)標(biāo)志,但隨著服役過程中其厚度的增加,會引起焊點(diǎn)中微裂紋萌生乃至斷裂。
當(dāng)其厚度超過某一臨界值時(shí),金屬間化合物會表現(xiàn)出脆性,而由于組成焊點(diǎn)的多種材料間的熱膨脹失配,使焊點(diǎn)在服役過程中會經(jīng)歷周期性的應(yīng)變,形變量足夠大時(shí)會導(dǎo)致失效。研究表明Sn60/Pb40軟釬料合金中加入微量稀土元素鑭,會減少金屬化合物的厚度,進(jìn)而使焊點(diǎn)的熱疲勞壽命提高2倍,顯著改善表面組裝焊點(diǎn)的可靠性。
3熱循環(huán)引起的失效
電子器件在服役條件下,電路的周期性通斷和環(huán)境溫度的周期性變化會使焊點(diǎn)經(jīng)受溫度循環(huán)過程。封裝材料問的熱膨脹失配,將在焊點(diǎn)中產(chǎn)生應(yīng)力和應(yīng)變。如在SMT中芯片載體材料A1203陶瓷的熱膨脹系數(shù)(CTE)為6×10-6℃-1,而環(huán)氧樹脂/玻璃纖維基板的CTE則為15×10-6℃-1。溫度變化時(shí),焊點(diǎn)將承受一定的應(yīng)力和應(yīng)變。一般焊點(diǎn)所承受應(yīng)變?yōu)?%~20%。在THT工藝中,器件的柔性引腳會吸收由于熱失配而引起的大部分應(yīng)變,焊點(diǎn)真正承受的應(yīng)變是很小的。而在SMT中,應(yīng)變基本由焊點(diǎn)來承受,從而會導(dǎo)致焊點(diǎn)中裂紋的萌生和擴(kuò)展,最終失效。
[page]
由于焊點(diǎn)是因熱膨脹系數(shù)不匹配產(chǎn)生熱應(yīng)力而開裂并導(dǎo)致失效,所以提高無引線元件與基板材料的熱匹配最容易成為人們首先關(guān)注的問題。目前已研究開發(fā)出42%Ni-Fe合金(CTE=5×10-6℃-1)、Cu-36%Ni-Fe合金(銦瓦合金)、Cu-Mo-Cu及石英纖維復(fù)合材料等新材料,其中Cu-銦瓦-Cu復(fù)合基板改變其中各成份比例,用此基板鉛焊的焊件經(jīng)1500次熱沖擊實(shí)驗(yàn),無焊點(diǎn)失效。另外還開發(fā)了在印制板上復(fù)合一層彈性較大的應(yīng)力吸收層,用以吸收由于熱失配引起的應(yīng)力等方面的技術(shù),也取得了比較好的效果。但新型基板材料的工藝復(fù)雜,價(jià)格相對昂貴,其實(shí)用性受到一定限制。
影響無鉛焊點(diǎn)可靠性的因素
1對無鉛焊料的性能要求
傳統(tǒng)錫鉛焊料因具有價(jià)廉、易焊接、成形美觀以及物理、力學(xué)和冶金性能好等特點(diǎn)而作為連接元器件和印刷電路板的標(biāo)準(zhǔn)材料,并形成了一整套的使用工藝,長期以來深受電子廠商的青睞。但由于鉛及鉛化合物對人類健康和生活環(huán)境的不利影響,限制和禁止使用含鉛焊料的呼聲日益高漲,各國政府紛紛制定相應(yīng)的法規(guī)約束電子產(chǎn)品的使用材料和廢棄物的處理,電子封裝的環(huán)境友好化要求已成為全球趨勢。因此目前電子行業(yè)全面面臨無鉛化的要求,已經(jīng)對整個(gè)行業(yè)形成巨大沖擊。近幾年無鉛焊料迅速發(fā)展起來,最常用的是Sn-Ag-Cu系列。
微電子領(lǐng)域使用的焊料有著很嚴(yán)格的性能要求,無鉛焊料也不例外,不僅包括電學(xué)和力學(xué)性能,還必須具有理想的熔融溫度。從制造工藝和可靠性兩方面考慮,表1列出了焊料合金的一些重要性能。
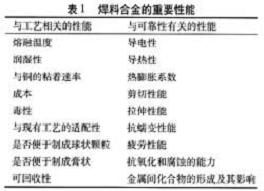
2影響無鉛焊點(diǎn)可靠性的因素
與傳統(tǒng)的含鉛工藝相比,無鉛化焊接由于焊料的差異和工藝參數(shù)的調(diào)整,必不可少地會給焊點(diǎn)可靠性帶來一定的影響。首先是目前無鉛焊料的熔點(diǎn)較高,一般都在217℃左右,而傳統(tǒng)的Sn-Pb共晶焊料熔點(diǎn)是183℃,溫度曲線的提升隨之會帶來焊料易氧化及金屬間化合物生長迅速等問題。其次是由于焊料不含Pb,焊料的潤濕性能較差,容易導(dǎo)致產(chǎn)品焊點(diǎn)的自校準(zhǔn)能力、拉伸強(qiáng)度、剪切強(qiáng)度等不能滿足要求。以某廠商為例,原含鉛工藝焊點(diǎn)不合格率一般平均在50×10-6(0.05%)左右,而無鉛工藝由于焊料潤濕性差,不合格率上升至200×10-6~500×10-6(0.2~0.5%)。
鑒于無鉛化焊點(diǎn)可靠性方面目前仍存在許多問題,有必要對此進(jìn)行分析。無鉛焊點(diǎn)的可靠性問題主要來源于:焊點(diǎn)的剪切疲勞與蠕變裂紋[7,8,9]、電遷移[8,10]、焊料與基體界面金屬間化合物形成裂紋[7,8,11,12]、Sn晶須生長引起短路[7,8],電腐蝕和化學(xué)腐蝕問題r¨等。以下我們主要從設(shè)計(jì)、材料與工藝角度介紹影響無鉛焊點(diǎn)可靠性的一些因素。
(1)設(shè)計(jì):PCB的合理設(shè)計(jì)問題。如焊盤設(shè)計(jì)不合理、發(fā)熱量大的元件密集分布、相鄰高大元件在回流焊時(shí)產(chǎn)生“高樓效應(yīng)”、形成熱風(fēng)沖擊等。
(2)材料:焊料的選擇極為重要。目前,大多采用錫銀銅合金系列,液相溫度是217℃-221℃,這就要求再流焊具有較高的峰值溫度,如前所述會帶來焊料及導(dǎo)體材料(如Cu箔)易高溫氧化、金屬間化合物生長迅速等問題。因?yàn)樵诤附舆^程中,熔融的釬料與焊接襯底接觸時(shí),由于高溫在界面會形成一層金屬間化合物(IMc)。其形成不但受回流焊溫度、時(shí)間的控制,而且在后期使用過程中其厚度會隨時(shí)間增加。
研究表明界面上的金屬間化合物是影響焊點(diǎn)可靠性的一個(gè)關(guān)鍵因素。過厚的金屬間化合物層的存在會導(dǎo)致焊點(diǎn)斷裂、韌性和抗低周疲勞能力下降,從而導(dǎo)致焊點(diǎn)的可靠性降低。以當(dāng)前最為成熟的Sn-Ag系無鉛焊料為例,由于熔點(diǎn)更高,相應(yīng)的再流焊溫度也將提高,加之無鉛焊料中Sn含量都比Sn-Pb焊料高,這兩者都增大了焊點(diǎn)和基體間界面上形成金屬問化合物的速率,導(dǎo)致焊點(diǎn)提前失效。
另外,由于無鉛焊料和傳統(tǒng)Sn-Pb焊料成分不同,因而它們和焊盤材料,如Cu、Ni、AgPd等的反應(yīng)速率及反應(yīng)產(chǎn)物可能不同,焊點(diǎn)也會表現(xiàn)出不同的可靠性。同時(shí)焊料和助焊劑的兼容性也會對焊點(diǎn)的可靠性產(chǎn)生非常大的影響。有研究表明:焊料和助焊劑各成分之間不兼容會導(dǎo)致附著力減小。此外,由于熱膨脹系數(shù)不匹配,又會加快焊料周期性的疲勞失效。因此要特別注意選擇兼容性優(yōu)良的焊料和助焊劑,才能耐受住無鉛再流焊時(shí)的高溫沖擊。
另外,各互連焊接部件均來自于不同生產(chǎn)廠商,因而部件質(zhì)量難免參差不齊,如器件引腳可焊性不良等,對無鉛工藝焊點(diǎn)可靠性有較大影響。比較典型的例子是.PCB板焊盤質(zhì)量問題。由于以前的熱風(fēng)整平(HASL)焊盤涂層工藝存在一些缺點(diǎn),因此目前OEM廠商應(yīng)用較廣泛的包括有機(jī)可焊性保護(hù)層(OSP)和Ni/Au涂層工藝。
其中Ni/Au涂層又有浸金法和鍍金法兩種,浸金法由于工藝簡單而較受國內(nèi)廠商青睞,但此法難于控制Au層厚度,常會出現(xiàn)Au層厚度不足導(dǎo)致其下的Ni層氧化,影響回流焊接時(shí)焊點(diǎn)的性能。對于此種情況,廠商一般可用俄歇電子能譜儀(AES)精確測量PCB焊盤的Au層厚度是否符合規(guī)格。
[page]
(3)工藝:在SMT、MCM制作工藝過程中,通常會遇到諸如焊料儲存溫度不當(dāng)、焊盤焊料不足、再流焊溫度曲線設(shè)置不當(dāng)?shù)葐栴}。就無鉛焊接而言,再流焊工藝溫度曲線的優(yōu)化至為重要,優(yōu)良的工藝既可保證形成高可靠性的焊接,又保持盡可能低的峰值溫度。
因此,目前除日本以外,其他國家的消費(fèi)電子公司似乎都接受了錫銀銅合金系列,合金中銀所占比例為3.0%~4.7%,銅為0.5%-3.0%。不同成分的合金熔點(diǎn)相差不大,基本上在217℃-221℃之間,而錫鉛合金(63%的錫和37%的鉛)的液相溫度是183℃,兩者相差34℃。
因此嚴(yán)密監(jiān)控再流工藝中的關(guān)鍵變量,如峰值溫度、高于液相溫度的時(shí)間、浸漬時(shí)間、浸漬溫度以及由于選擇焊劑和焊膏而引起的斜坡速率,以確保再流焊過程保持1.33或高于1.33的Cpk。另外需注意的一點(diǎn)是含Bi無鉛焊料的使用問題。研究發(fā)現(xiàn),含Bi焊料與Sn-Pb涂層的器件接觸時(shí),回流焊后會生成Sn-Pb-Bi共晶合金,熔點(diǎn)只有99.6℃,極易導(dǎo)致焊接部位開裂的發(fā)生。因此對含Bi無鉛焊料的使用需注意器件涂層是否為Sn-Pb涂層。
另外,關(guān)于無鉛焊接工藝中出現(xiàn)的空洞問題14,15]??斩词腔ミB焊點(diǎn)在回流焊接中常見的一種缺陷,在BGA/CSP等器件上表現(xiàn)得尤為突出。由于空洞的大小、位置、所占比例以及測量方面的差異性較大,至今對空洞水平的安全性評估仍未統(tǒng)一。有經(jīng)驗(yàn)的工程師習(xí)慣將無較大空洞(小尺寸的空洞體積之和不超過焊點(diǎn)體積的0.5%)、空洞比例低于15%~20%,且不集中于連接處的空洞歸于回流焊接中常見的一種缺陷,并認(rèn)為是可以接受的;
另一方面,按照Motorola的研究結(jié)果認(rèn)為直徑3μm~5μm的空洞事實(shí)上能提高焊點(diǎn)的長期可靠性,因?yàn)樗谝欢ǔ潭壬峡梢宰柚购更c(diǎn)中裂紋的擴(kuò)展。但一般認(rèn)為大的空洞,或空洞面積達(dá)到一定比例后會給可靠性帶來不利影響。
因此,在無鉛焊接中,空洞仍然是一個(gè)必須關(guān)注的問題。在熔融狀態(tài)下,Sn/Ag/Cu合金比Sn-Pb合金的表面張力更大,表面張力的增加勢必會使氣體在冷卻階段的外溢更加閑難,使得空洞比例增加。這一點(diǎn)在無鉛錫膏的研發(fā)過程中得到證實(shí),結(jié)果顯示使用無鉛錫膏的焊點(diǎn)中的空洞數(shù)量多于使用錫鉛錫膏的焊點(diǎn)。
大的空洞和一些小的球形空洞是由于助焊劑的揮發(fā)造成的,錫膏中助焊劑的配比是影響焊點(diǎn)空洞的最直接因素,因此無鉛錫膏仍有很大的改善空間。作為新一代的無鉛錫膏產(chǎn)品,Multicore(96SCLF32OAGS88)由于增加了助焊劑在高溫的活性,實(shí)現(xiàn)了技術(shù)上的長足飛躍,使得無鉛焊點(diǎn)的空洞水平可降低到7.5%左右。近兩年隨著材料研究方面的進(jìn)展,研制的第二代通用型無鉛焊膏除了具有更寬的工藝窗口、更容易應(yīng)用、有更好的外觀外,最為重要的是解決了空洞問題。
無鉛焊點(diǎn)可靠性測試方法
無鉛焊點(diǎn)可靠性測試,主要是對電子組裝產(chǎn)品進(jìn)行熱負(fù)荷試驗(yàn)(溫度沖擊或溫度循環(huán)試驗(yàn));按照疲勞壽命試驗(yàn)條件對電子器件結(jié)合部進(jìn)行機(jī)械應(yīng)力測試;使用模型進(jìn)行壽命評估。目前比較著名的模型有低循環(huán)疲勞的Coffin-Manson模型,一般在考慮平均溫度與頻率的影響時(shí)使用修正Coffin-Manson模型,而在考慮材料的溫度特性及蠕變關(guān)系時(shí)采用Coffin-Manson模型。
無鉛焊點(diǎn)可靠性測試方法主要有外觀檢查、X-ray檢查、金相切片分析、強(qiáng)度(抗拉、剪切)、疲勞壽命、高溫高濕、跌落實(shí)驗(yàn)、隨機(jī)震動(dòng)、可靠性檢測方法等。
外觀檢查:無鉛和有鉛焊接的焊點(diǎn)從外表看是有差別的,并影響AOI系統(tǒng)的正確性。無鉛焊點(diǎn)的條紋更明顯,并且比相應(yīng)的有鉛焊點(diǎn)粗糙,這是從液態(tài)到固態(tài)的相變造成的。因此這類焊點(diǎn)看起來顯得更粗糙、不平整。另外,由于無鉛焊料的表面張力較高,不像有鉛焊料那么容易流動(dòng),形成的圓角形狀也不盡相同。
因此檢測儀器必須做一些參數(shù)或程序調(diào)整,自動(dòng)光學(xué)檢測儀(AOI)制造商已經(jīng)推出了相應(yīng)的解決方案,其中包括歐姆龍采用三色光源和不同的照射角度將焊點(diǎn)的三維形狀用二維圖像表示出來,而安捷倫也在最近推出了采用固態(tài)建模(SSM)技術(shù)的三維自動(dòng)光學(xué)檢測設(shè)備等。
X-ray檢查:無鉛焊的球形焊點(diǎn)中虛焊增多。無鉛焊的焊接密度較高,可以檢測出焊接中出現(xiàn)的裂縫和虛焊。銅、錫和銀應(yīng)屬于“高密度”材料,為了進(jìn)行優(yōu)良焊接的特性表征、監(jiān)控組裝工藝,以及進(jìn)行最重要的焊點(diǎn)結(jié)構(gòu)完整性分析,有必要對X射線系統(tǒng)進(jìn)行重新校準(zhǔn),對檢測設(shè)備有較高要求。
準(zhǔn)自動(dòng)焊點(diǎn)可靠性檢測技術(shù)是利用光熱法逐點(diǎn)檢測電路板焊點(diǎn)質(zhì)量的一種先進(jìn)技術(shù),具有檢測精度高、可靠性好、檢測時(shí)不須接觸或破壞被測焊點(diǎn)等特點(diǎn)。檢測時(shí)對印制電路板的焊點(diǎn)逐點(diǎn)注入確定的激光能量,同時(shí)用紅外探測器監(jiān)測焊點(diǎn)在受到激光照射后產(chǎn)生的熱輻射。由于熱輻射特性與焊點(diǎn)的質(zhì)量狀況有關(guān),故可據(jù)此判定焊點(diǎn)的質(zhì)量好壞。激光與焊點(diǎn)的對準(zhǔn)和注入以及焊點(diǎn)質(zhì)量差別均由計(jì)算機(jī)及相應(yīng)的軟件完成。
測試裝置包括YJLG激光系統(tǒng)、紅外探測系統(tǒng)、X-Y掃描工作平臺以及由計(jì)算機(jī)控制的驅(qū)動(dòng)系統(tǒng)、閉路電視監(jiān)視系統(tǒng)、判讀軟件等五部分組成。此技術(shù)的焊點(diǎn)重缺陷檢出率為100%,,其他缺陷檢出率遠(yuǎn)高于人工檢測。檢測速度滿足小批量生產(chǎn)需要,特別適用于可靠性要求高、批量小的產(chǎn)品檢測。
在無鉛工藝焊點(diǎn)可靠性測試中,比較重要的是針對焊點(diǎn)與連接元器件熱膨脹系數(shù)不同進(jìn)行的溫度相關(guān)疲勞測試,包括等溫機(jī)械疲勞測試、熱疲勞測試及耐腐蝕測試等。其中根據(jù)測試結(jié)果可以確認(rèn)相同溫度下不同無鉛材料的抗機(jī)械應(yīng)力能力不同,同時(shí)有研究表明不同無鉛材料顯示出不同的失效機(jī)理,失效形態(tài)也各不相同。
對制造商來說,可靠性屬于比較高層次的考慮因素,但優(yōu)良的制造工藝方面還是最重要的,沒有先進(jìn)的制造工藝就沒有較高的可靠性。所以改進(jìn)材料和工藝是解決采用無鉛焊所出現(xiàn)的可靠性和失效缺陷的關(guān)鍵。
焊點(diǎn)在微電子封裝產(chǎn)業(yè)中起著舉足輕重的作用,相關(guān)設(shè)計(jì)、工藝均應(yīng)引起充分重視。積極優(yōu)化焊接工藝、找出失效模式、分析失效機(jī)理、提高產(chǎn)品質(zhì)量和可靠性水平,對電子封裝產(chǎn)業(yè)均有重要的意義。
無鉛焊點(diǎn)由于焊料的差異和焊接工藝參數(shù)的調(diào)整,必不可少地會給焊點(diǎn)可靠性帶來新的問題。我們從設(shè)計(jì)、材料及工藝角度分析了影響無鉛焊點(diǎn)可靠性的因素,如金屬間化合物厚度增加、材料的熱匹配問題、空洞問題、可靠性測試參數(shù)的改變等。
無鉛化技術(shù)已經(jīng)日趨成熟,但是在無鉛化進(jìn)程中還存在一些懸而未決的問題,如焊點(diǎn)的剪切疲勞、蠕變問題、虛焊現(xiàn)象、焊點(diǎn)熱疲勞的主要變形機(jī)制、焊點(diǎn)的顯微結(jié)構(gòu)對焊點(diǎn)的疲勞行為的影響與作用機(jī)制等,都有待進(jìn)一步研究。
去焊接工藝與測試社區(qū)看看